CAD Engineer Interview Questions with Answers
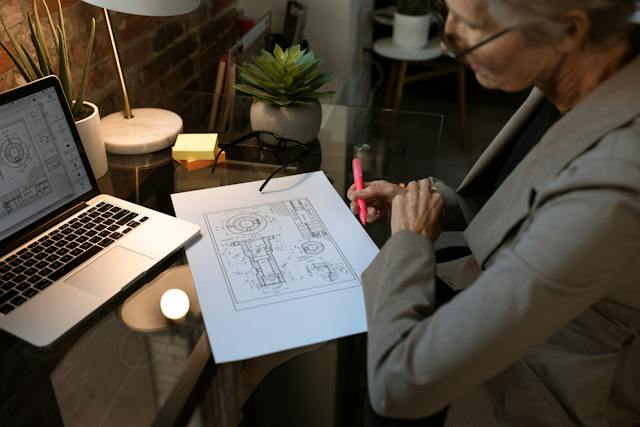
This page is a comprehensive resource for both hiring managers and job seekers, focusing on CAD Engineer interview questions and their sample answers. It provides an in-depth look at the essential skills, experiences, and problem-solving abilities required for a CAD Engineer role.
This guide covers questions on technical expertise, project management, collaboration, and innovative thinking to assist hiring managers in effectively evaluating candidates and help job seekers thoroughly prepare for interviews. Whether you are hiring a skilled CAD Engineer or a candidate aiming to excel in your next job interview, the questions and answers presented here provide valuable insights and guidance.
List of Popular CAD (Computer-Aided Design) Software
General CAD Software
- AutoCAD: One of the most well-known and widely used CAD programs for 2D and 3D design and drafting.
- DraftSight: A professional-grade 2D CAD product for users who want a better way to read, write, and share DWG files.
- BricsCAD: A CAD package developed by Bricsys, offering functionalities similar to AutoCAD but at a lower cost.
- FreeCAD: An open-source parametric 3D CAD modeler, suitable for a wide range of uses in engineering and architecture.
- TinkerCAD: An easy-to-use, browser-based 3D design and modeling tool, particularly popular in education and among beginners.
- ZWCAD: A reliable and cost-effective CAD software compatible with DWG files, primarily used for AEC and MCAD industries.
Mechanical Design and Engineering
- SolidWorks: A solid modeling CAD software primarily used for mechanical design and engineering.
- Inventor: Autodesk’s CAD software for mechanical design, documentation, and product simulation.
- Creo (formerly Pro/ENGINEER): A parametric, integrated 3D CAD/CAM/CAE solution used in product design and manufacturing.
- Fusion 360: Also from Autodesk, this is a cloud-based 3D modeling, CAD, CAM, CAE, and PCB software platform for product design and manufacturing.
- Solid Edge: Developed by Siemens, a solid modeling, assembly modeling, and drafting software for mechanical and product design.
- Ansys SpaceClaim: A versatile 3D modeling software used for engineering and design, particularly in mechanical engineering, prototyping, and simulation.
- Alibre Design: A parametric 3D CAD solution for professional mechanical design and engineering.
- Onshape: A cloud-based CAD system that combines powerful 3D modeling tools with real-time collaboration features.
- IronCAD: A user-friendly, drag-and-drop 3D CAD software ideal for product design and mechanical engineering.
Architecture and Construction
- Revit: A building information modeling software for architects, structural engineers, and MEP engineers.
- Chief Architect: Specialized for residential and light commercial design, popular among architects and builders for creating detailed architectural designs.
- MicroStation: Developed by Bentley Systems, an engineering software used for architecture, engineering, and construction (AEC) projects.
- Vectorworks: A versatile CAD software particularly popular among architects, landscape designers, and event planners.
- ArchiCAD: A BIM software used by architects, designers, and planners for architectural design and documentation.
- Tekla Structures: A BIM software used for creating and managing 3D structural models in concrete and steel.
Industrial Design and Specialized Fields
- CATIA: A high-end CAD/CAM/CAE software suite used for product design and engineering, particularly in aerospace and automotive industries.
- NX (formerly Unigraphics): A high-end CAD/CAM/CAE software suite used in engineering, particularly for complex assemblies and industries like aerospace and automotive.
- Rhinoceros (Rhino): A 3D modeling software used in various fields such as architecture, industrial design, and multimedia design.
- SketchUp: A user-friendly 3D modeling tool commonly used in architecture, interior design, civil, and mechanical engineering.
CAD Engineer Interview Questions and Answers
Core CAD Features
- What are the primary features of AutoCAD?
- Answer: AutoCAD’s primary features include 2D drawing and drafting, 3D modeling and visualization, parametric constraints, various importing and exporting options, and extensive customization through APIs and LISP.
- How does BIM (Building Information Modeling) software like Revit differ from traditional CAD software?
- Answer: BIM software like Revit creates detailed 3D models with embedded component information, unlike traditional CAD, which focuses on geometric representations.
- What are the benefits of using cloud-based CAD software like Fusion 360?
- Answer: Benefits include remote accessibility, collaboration efficiency, reduced hardware dependency, automatic updates, and enhanced data management and security.
Parametric Design and Modeling Techniques
- How does SolidWorks handle parametric design?
- Answer: SolidWorks uses parametric design, allowing users to create models and assemblies that can be easily modified by changing dimensions or relationships, ensuring consistency and accuracy.
- What is the purpose of “constraints” in parametric CAD modeling?
- Answer: Constraints control dimensions and relationships between geometric entities, maintaining design intent even when dimensions change.
- What are the advantages of using parametric modeling?
- Answer: Parametric modeling allows quick design modifications by changing parameters, ensuring consistency, reducing errors, and allowing easy updates and scalability.
- What is the difference between surface modeling and solid modeling?
- Answer: Surface modeling focuses on creating complex surfaces and curves, while solid modeling involves creating 3D models of solid objects with defined mass properties.
- In SolidWorks, what is the difference between a “part” and an “assembly”?
- Answer: A “part” is a single 3D object, while an “assembly” is a collection of parts and/or subassemblies arranged in a specific manner.
Manufacturing, 3D Printing, and Analysis
- What are the key considerations when designing for manufacturability using CAD?
- Answer: Consider material selection, manufacturing processes, ease of assembly, part count reduction, and adherence to industry standards and tolerances.
- How do you optimize a design for 3D printing in CAD software?
- Answer: Optimize print orientation, support structures, wall thickness, tolerances, and material properties using CAD simulations to ensure successful printing.
- What is the significance of “geometric dimensioning and tolerancing” (GD&T) in CAD?
- Answer: GD&T defines and communicates engineering tolerances, ensuring precision and clarity in the design process with standardized symbols.
- How do you perform a stress analysis in CAD software?
- Answer: Use FEA (Finite Element Analysis) tools to define material properties, apply loads and constraints, and simulate stress distribution.
Usability, Ergonomics, and File Management
- How do you ensure that a CAD design is ergonomic and user-friendly?
- Answer: Consider human factors like size, shape, and interaction, using CAD simulations to analyze ergonomics.
- How do you handle file compatibility and version control in CAD?
- Answer: File compatibility is managed by using common file formats like DWG or DXF. Version control is handled through CAD software’s built-in systems or external version control systems.
Specialized CAD Software
- What are the key features of CATIA that differentiate it from other CAD software?
- Answer: CATIA offers advanced surface modeling, handles complex assemblies, integrates systems engineering, and has strong collaboration features.