Asset Management Interview Questions with Answers
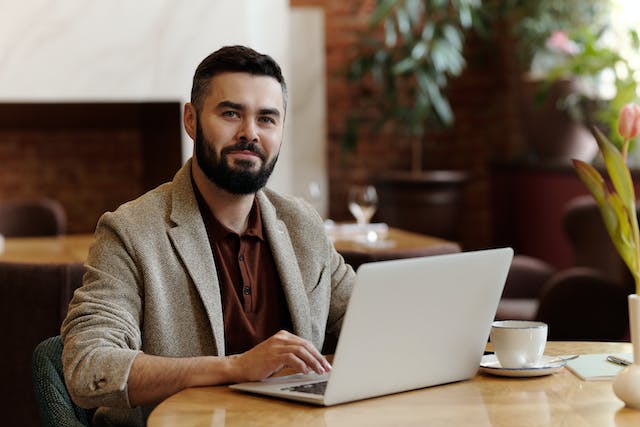
Inventory asset management is a critical component of supply chain operations, ensuring that inventory is tracked, managed, and optimized effectively. For professionals in this field, demonstrating expertise through a job interview can be a pivotal moment. Below are some tailored technical interview questions along with concise answers that hiring managers might ask and job seekers should be prepared to answer. These questions cover fundamental concepts, practical applications, and scenario-based problem solving.
What are some common inventory management metrics?
Important inventory metrics include:
- Inventory Turnover: Measures how often inventory is sold and replaced within a period.
- Carrying Cost of Inventory: Total cost of holding inventory, including storage, insurance, and depreciation.
- Order Accuracy: Percentage of orders shipped without errors.
- Stockout Rate: Frequency at which inventory is not available when demanded by a customer.
How does inventory management affect customer satisfaction?
Effective inventory management ensures products are available when customers need them, which enhances customer satisfaction by reducing wait times and preventing stockouts. It also helps maintain product quality by managing the storage conditions appropriately.
Explain the ABC analysis in inventory management.
ABC analysis categorizes inventory into three classes:
- A Items: High-value items with low sales frequency.
- B Items: Moderate value and sales frequency.
- C Items: Low value but high sales frequency. This method helps prioritize inventory management efforts based on the potential impact on overall inventory costs.
What is a safety stock, and how do you calculate it?
Safety stock is additional inventory held to prevent stockouts caused by unpredictable fluctuations in demand or supply. It is calculated based on factors like average lead time, average demand, and demand and supply variability.
How do you optimize inventory levels?
Optimizing inventory levels involves:
- Regular Audits: To ensure inventory accuracy.
- Demand Forecasting: To predict and respond to future consumption patterns.
- Lean Inventory Techniques: Such as JIT, which reduces excess inventory and associated costs.
- Supplier Management: To ensure reliable lead times and material quality.
What challenges have you faced in inventory management, and how did you overcome them?
A common challenge is managing inventory levels efficiently to avoid overstock and stockouts. I addressed this by implementing better forecasting tools and refining the supply chain logistics, which helped align inventory more closely with actual market demand.
Discuss the role of technology in modern inventory management.
Technology plays a crucial role in modern inventory management by providing tools like:
- ERP Systems: For integrating all facets of an operation, including inventory, accounting, and customer relations.
- RFID and IoT: For real-time tracking of inventory movements and conditions.
- Data Analytics: To analyze trends and improve decision-making processes regarding inventory control.
What impact does lead time have on inventory control?
Lead time, the delay between ordering and receiving inventory, directly affects inventory levels. Longer lead times require higher levels of safety stock to cover the period and prevent potential stockouts, thus impacting inventory costs and management strategies.
What is Just-In-Time (JIT) inventory management?
Just-In-Time (JIT) inventory management is a strategy aimed at increasing efficiency and reducing waste by receiving goods only as they are needed in the production process, thereby reducing inventory costs. This system requires accurate demand forecasting and strong supplier relationships to succeed.
How do you use inventory management software to improve efficiency?
Inventory management software improves efficiency by automating stock level monitoring, order placements, and tracking deliveries. It provides real-time data which helps in making informed decisions quickly, reducing manual errors, and enhancing communication across departments.
What are the risks associated with poor inventory management?
Risks include:
- Overstocking: Ties up capital and increases holding costs.
- Understocking: Leads to stockouts, potential sales loss, and customer dissatisfaction.
- Obsolete Inventory: Items become outdated, leading to write-offs.
- Inaccurate Records: Can cause production delays and misinformed decision-making.
Can you describe cycle counting and its benefits?
Cycle counting is a periodic counting of inventory items to ensure accuracy of stock records without halting daily operations. Benefits include:
- Improved Inventory Accuracy: Helps identify discrepancies early.
- Reduced Disruption: Unlike full inventory audits, cycle counting does not require shutting down sales or production.
- Enhanced Order Fulfillment: Accurate records help meet customer orders efficiently.
How would you manage excess inventory?
Managing excess inventory can be tackled through strategies like:
- Discounting Products: To accelerate sales.
- Bundling Products: Offering them in combinations to increase their appeal.
- Returning to Suppliers: If possible, for a refund or credit.
- Diversifying Sales Channels: Exploring new markets or online platforms.
What are the differences between perpetual and periodic inventory systems?
- Perpetual Inventory System: Continuously updates inventory records with each transaction, providing real-time inventory levels. It is typically used with barcode scanners and inventory management software.
- Periodic Inventory System: Updates inventory records at specific intervals, such as monthly or quarterly, which might not reflect current inventory levels accurately but is simpler and less costly to maintain.
How do you deal with inventory shrinkage?
Inventory shrinkage can be managed by:
- Implementing Tighter Security: To prevent theft.
- Regular Audits and Reconciliations: To catch and correct discrepancies.
- Employee Training: To reduce errors in inventory handling and recording.
- Improved Inventory Tracking: Using RFID tags and other technology to monitor stock movements.
What role does supplier relationship management play in inventory management?
Supplier relationship management is crucial for:
- Ensuring Reliable Supply: Strong relationships can lead to more dependable lead times and priority service.
- Negotiating Better Terms: Such as pricing, delivery schedules, and payment terms.
- Quick Resolution of Issues: Good communication helps resolve delays and quality issues faster.
How do cycle counts differ from physical inventory counts?
Cycle counting involves regularly scheduled counting of parts of the inventory, allowing for continuous verification and updates without disrupting operations. Physical inventory counts typically occur annually, requiring operations to pause while every item is counted, which ensures system accuracy but can be disruptive.
What are the advantages of using an Automated Storage and Retrieval System (ASRS)?
The advantages of using an Automated Storage and Retrieval System (ASRS) include:
- Increased Storage Density: Maximizes space utilization through high-density configurations.
- Enhanced Retrieval Efficiency: Reduces retrieval times with automated processes.
- Improved Inventory Accuracy: Minimizes human errors in picking and placing.
- Labor Cost Savings: Reduces the need for manual labor in storage and retrieval tasks.
How do you handle inventory for seasonal products?
Managing inventory for seasonal products involves:
- Accurate Demand Forecasting: Using historical sales data to predict demand spikes and drops.
- Strategic Pre-Ordering: Placing orders well in advance to ensure adequate stock before the season starts.
- Post-Season Analysis: Reviewing what sold well or poorly to adjust future orders and clearance strategies.
Explain the concept of consignment inventory.
Consignment inventory is where goods are sent to a retailer or third party, but the ownership remains with the supplier until the items are sold. This arrangement reduces risk and storage costs for the retailer and allows suppliers to broaden their market reach without immediate sales.
What strategies would you use to reduce lead times in inventory supply?
Strategies to reduce lead times include:
- Supplier Collaboration: Working closely with suppliers to ensure they understand demand forecasts and can adjust their production schedules.
- Local Sourcing: Choosing suppliers closer to the production or sales site to reduce transportation time.
- Improving Internal Processes: Streamlining ordering and receiving processes to reduce delays within the company.
How important is inventory visibility and what tools help achieve it?
Inventory visibility is crucial for managing stock levels accurately and responding swiftly to supply chain dynamics. Tools that enhance visibility include:
- ERP Systems: Provide real-time data across different departments and locations.
- RFID Technology: Offers instant data on the movement and status of inventory items.
- Cloud-Based Inventory Management Software: Allows for access to inventory data from anywhere, facilitating better decision-making.
Describe how you would use data analytics in inventory management.
Data analytics can be used in inventory management to:
- Identify Trends: Analyze sales data to predict future demand patterns.
- Optimize Stock Levels: Use predictive analytics to maintain optimal inventory levels, reducing overstock and stockouts.
- Improve Supplier Performance: Analyze supplier delivery times and quality metrics to negotiate better terms or make changes.
What is the impact of poor inventory accuracy on a business?
Poor inventory accuracy can lead to:
- Increased Costs: Due to overstocking or expedited shipping to cover shortages.
- Lost Sales: From stockouts or inability to meet customer demand promptly.
- Reduced Customer Satisfaction: Resulting from incorrect order fulfillment or delayed shipments.
Common Technologies Used in Inventory Asset Management
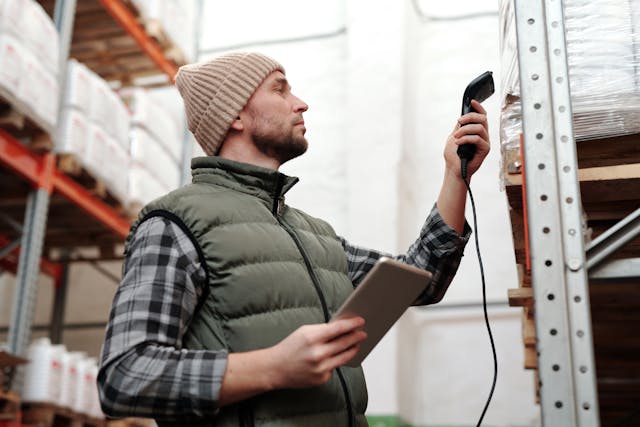
Inventory asset management leverages various technologies to enhance accuracy, efficiency, and real-time data accessibility. Here are some of the most commonly used technologies in this field:
- ERP Systems (Enterprise Resource Planning): These systems integrate all facets of an enterprise into one comprehensive information system that can be accessed by individuals across an organization. Examples include SAP, Oracle, and Microsoft Dynamics.
- Barcode Scanners: Used to automate data entry into inventory systems. Barcode technology improves the speed and accuracy of inventory control.
- RFID (Radio Frequency Identification): Offers advanced tracking capabilities by using radio waves to read and capture information stored on a tag attached to an item. RFID tags do not require line-of-sight to be read, unlike barcodes.
- Inventory Management Software: Specialized software designed to monitor inventory levels, orders, sales, and deliveries. Popular options include Zoho Inventory, NetSuite, and Fishbowl.
- Automated Storage and Retrieval Systems (ASRS): These are robotic systems that automatically place or retrieve loads from defined storage locations, improving efficiency and reducing labor costs.
- IoT (Internet of Things): IoT devices can track inventory in real-time and monitor conditions within storage areas, such as temperature or humidity, that might affect the product.
- Cloud-Based Platforms: Cloud solutions allow businesses to access their inventory data from anywhere, facilitating better collaboration and data sharing across locations.
- Data Analytics Tools: Tools like Power BI or Tableau help analyze vast amounts of inventory data to identify trends, forecast demand, and optimize inventory levels.
- Mobile Inventory Management Applications: Mobile apps enable warehouse managers and staff to update and access inventory data from anywhere in the warehouse, enhancing flexibility and immediacy of information.
- Supply Chain Management Software: Integrates inventory management with other supply chain functions, providing a holistic view and control over the entire supply chain.
Key Expertise Areas in Inventory Asset Management
Inventory asset management requires a blend of specific skills and knowledge to effectively control and optimize inventory processes. Here are some common areas of expertise used in this field:
- Inventory Forecasting: Ability to predict inventory needs based on historical data, market trends, and seasonal fluctuations to ensure optimal stock levels.
- Supply Chain Coordination: Understanding the integration of supply and demand management across multiple locations and coordinating effectively with suppliers and logistics.
- Data Analysis: Proficiency in analyzing inventory data to identify trends, perform root cause analysis of inventory issues, and make informed decisions.
- Financial Acumen: Understanding of the financial implications of inventory decisions, including cost analysis, budgeting, and the economic impact of inventory levels.
- Regulatory Compliance: Knowledge of and adherence to relevant laws and regulations that affect inventory management, such as safety standards and import-export restrictions.
- Process Improvement: Skills in identifying inefficiencies in inventory processes and implementing more effective systems and technologies.
- Technology Utilization: Expertise in using specific inventory management software, ERP systems, and emerging technologies like RFID and IoT to enhance inventory tracking and management.
- Risk Management: Ability to identify potential risks in inventory levels and supply chain processes and develop strategies to mitigate these risks.
- Project Management: Skills in managing projects related to inventory optimization, system upgrades, or implementation of new inventory management systems.
- Customer Service Orientation: Ensuring that inventory management practices align with customer requirements and contribute to high service levels and customer satisfaction.
Need to Hire?
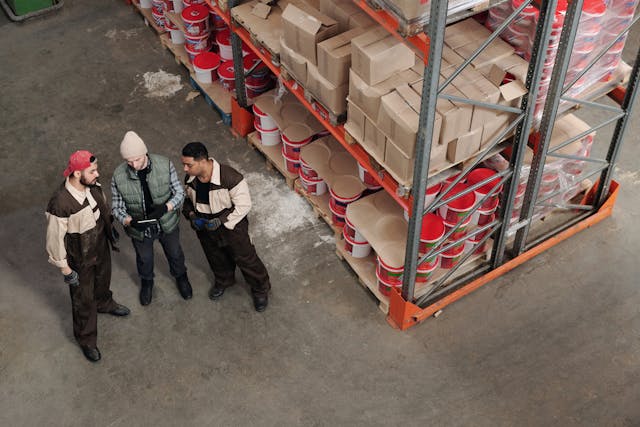
If you’re looking to enhance your inventory asset management team, Tier2Tek Staffing can connect you with top-tier professionals who specialize in optimizing and managing your inventory effectively. Our experts are adept at navigating complex inventory systems to ensure your operations are seamless and efficient.